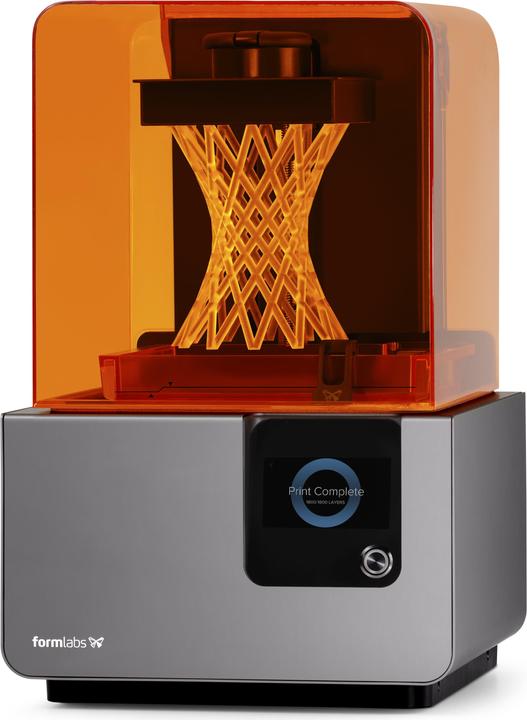

Un aperçu des technologies d'impression 3D les plus courantes

La plupart des imprimantes 3D que vous pouvez acheter aujourd'hui en tant que particulier sont basées sur la technologie de fabrication par filament fondu. Pourtant, cette norme est loin d'être la seule.
Nous sommes en 1966 et la télévision diffuse une nouvelle série étrange dans laquelle les personnages principaux se promènent en pyjama. Star Trek envahit les foyers américains. Outre les extraterrestres et les escapades romantiques du capitaine James Tiberius Kirk, les téléspectateurs voient une étrange machine utilisée par l'équipage de l'Enterprise pour synthétiser de la nourriture, des vêtements et des pièces détachées. L'idée de l'impression 3D s'imprime ainsi dans la mémoire collective.
Il faudra cependant attendre un peu moins de vingt ans pour que le premier brevet d'impression 3D soit déposé. En 1984, Chuck Hull dépose une demande de brevet pour la stéréolithographie, qui est acceptée en 1986. L'impression 3D est née. Par la suite, de plus en plus de technologies de fabrication additive se développent. Le terme anglais Additive Manufacturing, ou AM, est souvent utilisé. Je vais vous présenter trois de ces technologies de manière plus détaillée.
La stéréolithographie (SLA)
La stéréolithographie (SLA) est considérée comme le premier procédé d'impression 3D. La SLA est un processus basé sur le laser qui utilise des résines photopolymères. L'imprimante est alimentée en données 3D. Un faisceau laser UV est ensuite dirigé sur les axes X et Y sur la surface de la résine, ce qui permet à la résine de durcir exactement à l'endroit où le laser frappe la surface. L'imprimante fait de même, couche par couche, sur l'axe Z.
Lorsqu'une pièce SLA est terminée, elle est placée dans un solvant. Cela permet d'éliminer la résine humide qui reste à la surface de la pièce ou qui a été imprimée comme structure de support. Elle est ensuite placée dans un four à UV pour la durcir et terminer le processus d'impression.
L'épaisseur minimale de la couche d'un composant SLA est typiquement de 0,05 mm. Cette technologie offre la finition de surface la plus lisse de tous les processus de fabrication additive. Compte tenu du niveau de qualité que le SLA peut atteindre, il est particulièrement utile pour créer des modèles de moulage par impression 3D de haute précision, du plus petit au plus grand, rapidement et à moindre coût.
Les propriétés mécaniques des matériaux SLA sont vastes et offrent une grande variété d'applications. En particulier, les pièces nécessitant des propriétés similaires à celles de l'ABS ou du polypropylène s'impriment très bien en SLA.
Les matériaux SLA les plus courants sont les suivants :
- Résine standard : idéale pour les prototypes avec un état de surface détaillé .- Résine technique : idéale pour les applications à haute température .- Résine coulable : idéale pour les applications de moulage à la cire perdue .- Résine dentaire : très résistante et précise pour les applications dentaires .
Le traitement numérique de la lumière
Le DLP (Digital Light Processing) est un procédé similaire à la stéréolithographie. Il utilise également des photopolymères. La principale différence réside dans la source de lumière. Le DLP utilise une source lumineuse plus conventionnelle - comme une lampe à chambre noire
. - qui est appliquée en un seul passage sur toute la surface du bac en résine photopolymère. Cela rend le processus d'impression plus rapide SLA.
Dans ce processus, une fois que le modèle 3D a été envoyé à l'imprimante, un bac de polymère liquide est exposé à la lumière d'un projecteur DLP. Le projecteur DLP affiche l'image du modèle 3D sur le polymère liquide. Le polymère liquide exposé durcit et la plaque de construction se déplace vers le bas. La couche suivante de polymère liquide est à nouveau exposée à la lumière. Le processus est répété jusqu'à ce que le modèle 3D soit complet et que le réservoir soit vidé.
Comme l'impression SLA, la DLP nécessite des structures de support pour certaines pièces, en particulier celles qui présentent des surplombs ou des contre-dépouilles. Ces structures doivent être retirées manuellement. Les objets 3D doivent être nettoyés et durcis en post-traitement. Lors de la polymérisation, la pièce est exposée à une lumière intense dans une machine semblable à un four afin de polymériser complètement la résine.
Modélisation par dépôt de filament fondu et fabrication de filament fondu
. L'impression 3D, qui consiste à extruder un matériau thermoplastique, est de loin le procédé d'impression 3D le plus courant et le plus connu. Le nom le plus connu pour ce processus est Fused Deposition Modelling (FDM). Vous vous êtes peut-être déjà demandé quelle était la différence entre FDM et Fused Filament Fabrication (FFF). La réponse courte : il n'y en a pas. La réponse longue : la société Stratasys, qui détient plusieurs brevets sur le procédé, a déposé le terme FDM dès 1991. Les membres du projet RepRap ont développé le terme FFF comme alternative au terme FDM.
C'est grâce à FFF que l'impression 3D est devenue accessible au consommateur lambda. C'est ainsi que vous trouverez le plus grand nombre d'imprimantes FFF dans l'assortiment de digitec. Cette situation est principalement due au projet RepRap. RepRap est l'abréviation de Replicating Rapid rototyper. Il s'agit d'une machine qui se reproduit elle-même. L'objectif est de fabriquer d'autres imprimantes 3D à l'aide d'imprimantes 3D. Le modèle le plus connu est la Prusa i3. Les plans de cette dernière sont librement accessibles et vous pouvez la bricoler vous-même. Je ne sais pas pour vous, mais c'est ce que j'ai envie d'essayer.
Le procédé fonctionne en faisant fondre des filaments de plastique. L'imprimante les dépose sur une plateforme de construction selon les données 3D fournies à l'imprimante. Chaque couche durcit lorsqu'elle est pressée et se lie à la couche précédente. Les processus FDM/FFF nécessitent des structures de support pour certains modèles en surplomb.
Le grand avantage du FFF est la durabilité des matériaux, la stabilité de leurs propriétés mécaniques dans le temps et la qualité des pièces. Les thermoplastiques utilisés dans le FDM conviennent aux prototypes fonctionnels détaillés, aux outils de fabrication durables et aux pièces produites en petites séries. Cependant, contrairement aux procédés d'impression SLA et DLP, les couches sont légèrement plus épaisses, généralement au minimum 0,1 mm, ce qui les rend moins précises.
Autres avantages du FFF:
- Grand choix de matériaux, dont de nombreux thermoplastiques courants, des thermoplastiques à base de bois et de métal fondu et même des aliments (comme le chocolat)
- La technologie d'impression la plus économique .- Les matériaux d'impression les moins chers .- Un changement de matériau facile .- Il est possible d'imprimer avec différents matériaux .- Relativement facile de construire sa propre imprimante
- Impression rapide .
Les principaux inconvénients du FFF sont les suivants:
- Les détails des impressions finales sont limités par la taille de la buse. D'autres technologies offrent des détails plus précis .- La résistance des pièces finies est limitée car chaque couche est liée à la couche sous-jacente .
Plastic Jet Printing ou PJP est une autre technologie d'impression 3D qui utilise la chaleur et la pression pour extruder du plastique en continu. Mais contrairement au FFF, les thermoplastiques sont les seuls matériaux utilisés dans l'impression 3D PJP.
Hier geht's zu allen FFF-Druckern.


La technologie et la société me fascinent. Combiner les deux et les regarder sous différents angles est ma passion.